The slots, sockets, connectors and capacitors that were plugged into the board on the manual assembly
line now need to be soldered to the motherboard. Manual soldering would be
too time consuming, so Gigabyte makes use of a special
soldering process called wave soldering.
This imposing piece of mechanics is the final step on
the conveyor belt that runs through the manual assembly lines. It runs the
bottom of each motherboard through a 'wave' of liquid solder (induced
by flowing the molten solder over a raised ledge) at a
precise height, so that the metal leads of the plugged-in components are
coated with solder. Each board passes through this wave for 2-4 seconds, after which it is
allowed to cool naturally so the solder can solidify around the contacts.
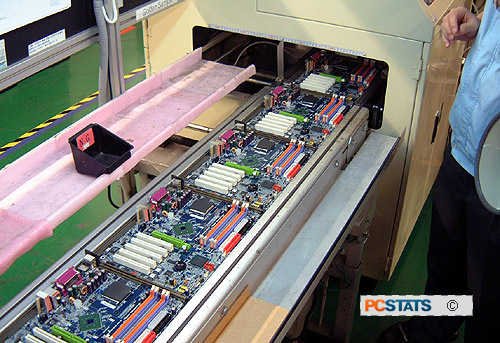 About to go
into the solder wave machine. |
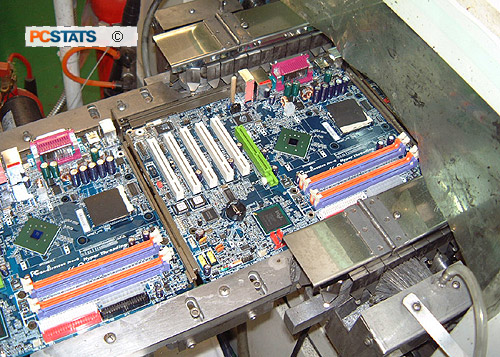 Note the lead
weight on the socket. This stops it floating up in the solder
|
Larger sockets sometimes have a tendency to float up a
little, so small lead weights are used to hold these sockets down.
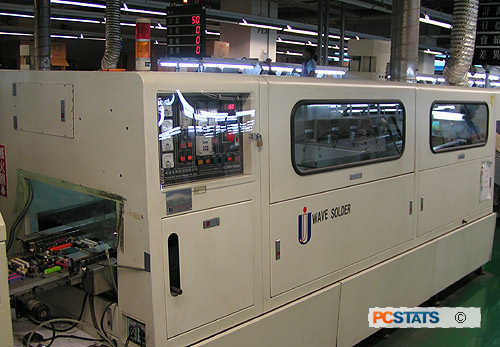 The wave
solder reflow machine |